Liquid storage solutions are the backbone of countless industrial operations. Whether it’s storing fuel at a power plant, safely housing corrosive chemicals in a manufacturing facility, or preserving perishable ingredients at a food processing plant, the design of these systems must be highly customized. Each industry comes with distinct demands around materials, safety, regulation, temperature control, and long-term performance. What works for one application could be entirely unsuitable for another. This is why thoughtful, industry-specific planning is critical in every aspect of system design.
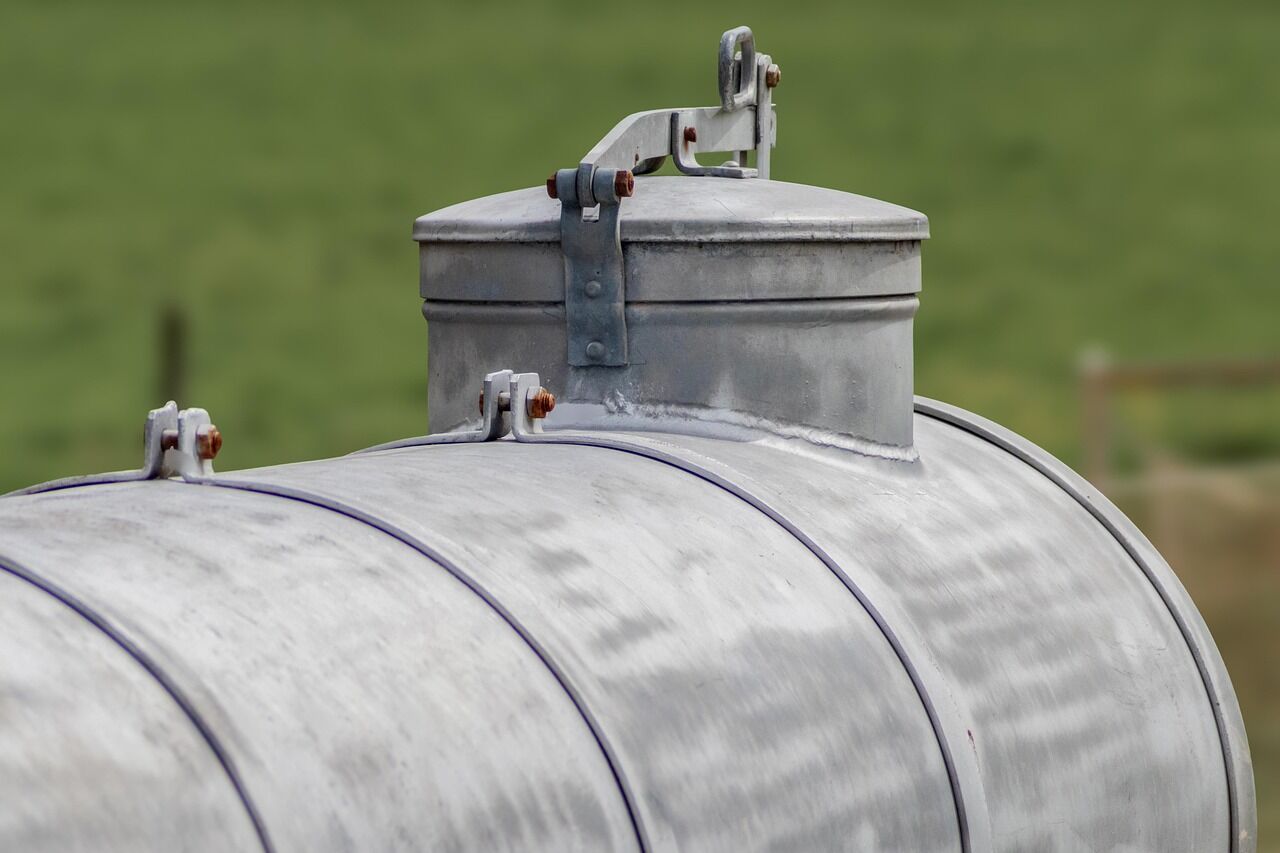
Why Industry Demands Influence Every Design Choice
Different sectors handle different types of liquids, ranging from flammable fuels to sterile water or viscous sludges, and each has its own operational and regulatory expectations. A water treatment plant, for instance, must prioritize chemical resistance and environmental protection, while a dairy production facility must emphasize hygiene and rapid cleaning. These contrasting requirements affect everything from material selection to maintenance cycles.
The level of precision required varies widely. A pharmaceutical plant may need extremely tight control over storage conditions, while an agricultural operation may tolerate more variability. These fundamental differences have led engineers to develop highly specialized tanks and liquid storage systems that align with the needs of individual industries. The design process starts by analyzing the chemical properties, handling requirements, and environmental exposure risks associated with the stored liquid.
Material Selection Based on Compatibility and Corrosion Risk
The chemical composition of stored liquids is the single most important factor in choosing tank materials. Some industries handle corrosive acids, reactive solvents, or biohazardous fluids that can eat through common construction materials. In chemical manufacturing and wastewater treatment, for example, materials like fiberglass-reinforced plastic (FRP), HDPE, or rubber-lined steel are often used to prevent corrosion and maintain structural integrity.
Meanwhile, food and beverage facilities need FDA-approved materials such as sanitary-grade stainless steel that resist microbial contamination and are easy to clean. A petroleum storage tank may use carbon steel but include corrosion-inhibiting coatings or cathodic protection systems. In every case, choosing the wrong material shortens equipment life and can lead to dangerous leaks and costly compliance failures.
Capacity Planning and Volume Requirements
The size of the operation directly affects the volume of liquid that needs to be stored at any given time. Industrial-scale facilities may require tanks capable of storing hundreds of thousands of gallons, while small-batch production lines need more compact, modular systems that support easy relocation and integration.
Designers must balance available space, refill frequency, and demand cycles when determining storage capacity. Some systems require multiple connected tanks to separate batches, segregate chemicals, or provide redundancy. Others use a single, large containment unit designed for maximum efficiency. In either case, the volume of liquid handled each day helps define the system’s structure, cost, and complexity.
Thermal Management Requirements
Many industrial liquids are temperature-sensitive, meaning they require insulation, active heating, or cooling to maintain stability. The oil and gas sector frequently deals with high-temperature storage, necessitating heating elements and insulated tank walls to keep materials like asphalt or heavy crude in a flowable state. By contrast, the food and pharmaceutical industries may rely on jacketed tanks or refrigeration systems to keep contents cool and safe from bacterial growth.
Even industries that don't require exact temperature control may still need thermal protection against seasonal fluctuations. Insulated tanks and climate-controlled enclosures can prevent freezing, condensation, or heat-induced degradation. The choice of thermal regulation systems depends on both the liquid’s properties and the site’s ambient conditions.
Pressure and Flow Dynamics
In applications involving pressurized liquids or volatile compounds, storage tanks must be engineered to withstand internal pressure and control flow rates safely. This is common in beverage production, where carbonation levels must be maintained, and in energy sectors that manage gases and fuels under pressure.
High-viscosity liquids, such as sludge or resin, may require aggressive agitation or heating to remain fluid. For others, laminar flow and gentle pumping are needed to avoid product degradation. This has implications for the design of tank outlets, piping systems, and pump selection. Controlling flow affects metering, batching, and dispensing processes, all of which must align with operational needs.
Regulatory Compliance and Industry Standards
Every industry faces a unique web of compliance requirements that govern how liquids are stored and handled. Chemical facilities must meet OSHA and EPA standards for spill prevention, emissions control, and hazard mitigation. Food processing and pharmaceutical plants must follow strict hygiene standards from the FDA, USDA, or global counterparts.
Regulatory agencies often specify inspection intervals, secondary containment features, and documentation protocols. Dairy tanks must be accessible for routine sanitation, while fuel storage tanks require leak detection and emergency shutoff systems. Staying compliant with these diverse regulations requires close collaboration between design engineers, compliance officers, and industry experts.
Integration of Automation and Remote Monitoring
Industries increasingly demand smart storage options that integrate with broader digital infrastructure. Real-time monitoring of temperature, pressure, fill levels, and leak detection has become the norm rather than the exception. This data is used for safety and to improve efficiency, reduce waste, and maintain product integrity.
Supervisory Control and Data Acquisition (SCADA) systems are common in water treatment and energy applications, where constant oversight is necessary. The pharmaceutical and chemical industries benefit from integrated systems that control dosing, track batch performance, and automate safety alerts. The ability to tie the systems into ERP or inventory platforms offers valuable insights and allows for predictive maintenance, lowering long-term costs.
Location and Site-Specific Considerations
Where a tank is placed can significantly impact its design and construction. Outdoor tanks must withstand UV radiation, temperature extremes, and precipitation. Tanks located in seismically active regions require special bracing or foundations. Coastal or marine environments may demand corrosion-resistant materials and coatings due to salt exposure.
Above-ground tanks are easier to access and inspect, but may be more vulnerable to environmental conditions. Underground tanks conserve space and offer aesthetic benefits, but require additional considerations for waterproofing and leak detection. Understanding the local environment ensures that the system is durable and practical for day-to-day use.
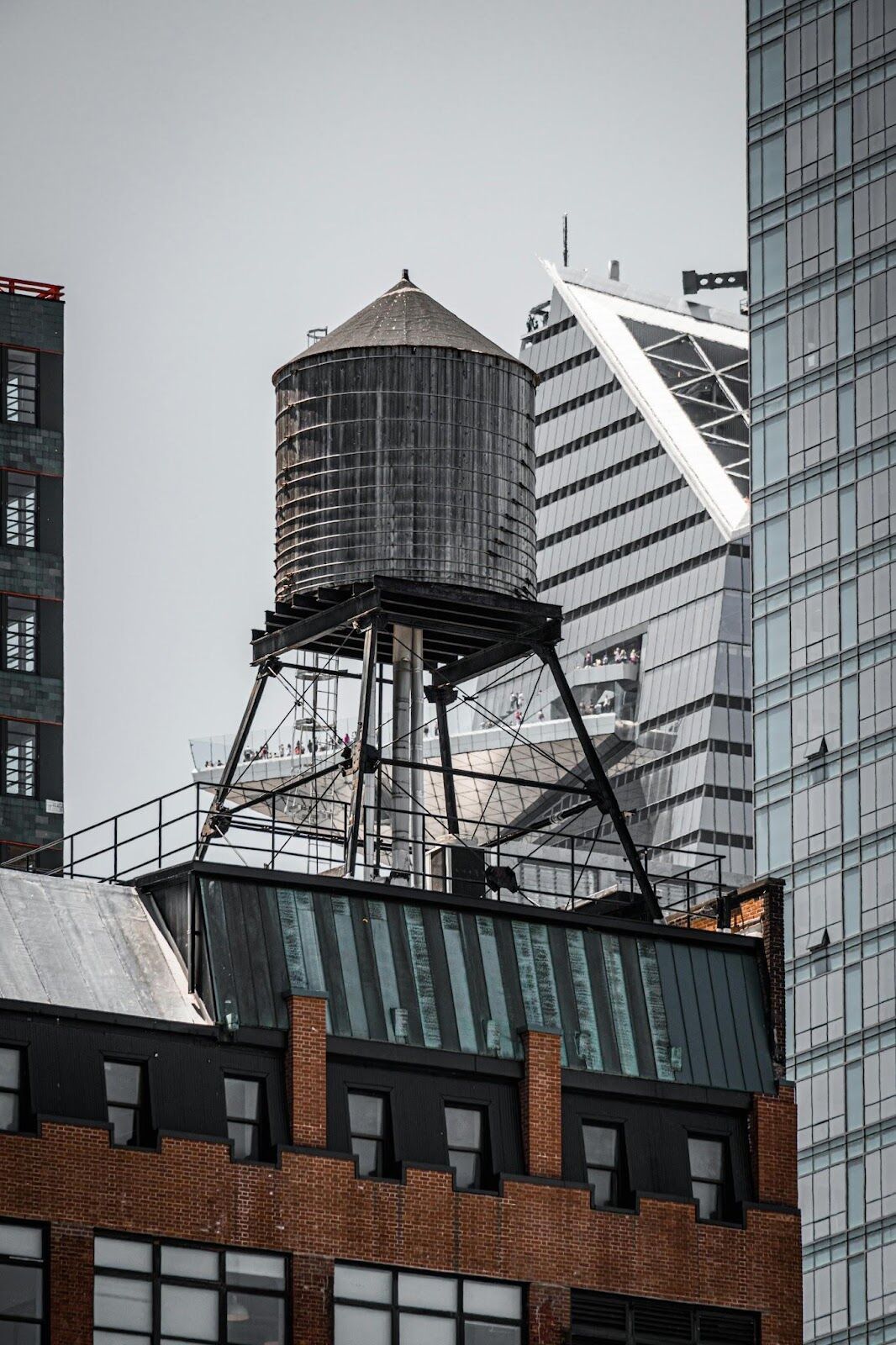
From material compatibility and temperature regulation to regulatory compliance and digital integration, liquid storage system design is deeply influenced by the specific needs of the industry it serves. Each sector brings its own set of challenges, operational goals, and safety concerns that must be addressed at the planning stage. Customization is not a luxury, it’s a necessity to ensure efficiency, reliability, and regulatory alignment.
Related Articles:
(0) comments
We welcome your comments
Log In
Post a comment as Guest
Keep it Clean. Please avoid obscene, vulgar, lewd, racist or sexually-oriented language.
PLEASE TURN OFF YOUR CAPS LOCK.
Don't Threaten. Threats of harming another person will not be tolerated.
Be Truthful. Don't knowingly lie about anyone or anything.
Be Nice. No racism, sexism or any sort of -ism that is degrading to another person.
Be Proactive. Use the 'Report' link on each comment to let us know of abusive posts.
Share with Us. We'd love to hear eyewitness accounts, the history behind an article.