
Precision gearboxes represent a critical component in the realm of mechanical engineering, playing a pivotal role in various industrial and commercial applications. These highly specialized gear systems are designed to deliver exceptional accuracy and efficiency, ensuring that machinery operates smoothly and reliably. In this article, we delve into the intricacies of precision gearbox design, explore their functionality, and examine their profound impact on modern machinery.
Crafting Precision with Engineering Excellence
The design of precision gearboxes is a sophisticated process that demands meticulous attention to detail and an in-depth understanding of mechanical principles. Engineers must consider a multitude of factors, including gear ratio, torque capacity, and backlash, to create gearboxes that meet specific performance criteria. The selection of materials is paramount; high-quality alloys and composites are often chosen for their strength, durability, and resistance to wear. Advanced manufacturing techniques, such as CNC machining and additive manufacturing, are employed to achieve the precise tolerances required for optimal performance.
Moreover, the internal configuration of precision gearboxes can vary significantly depending on the intended application. Planetary gear systems, for instance, are renowned for their high torque density and compact design, making them ideal for use in robotics and aerospace applications. Harmonic drive gearboxes, on the other hand, offer unparalleled positional accuracy and are frequently utilized in semiconductor manufacturing equipment. Each type of gearbox is meticulously engineered to balance efficiency, load capacity, and longevity, ensuring they can withstand the rigorous demands of their respective industries.
Ensuring Smooth and Accurate Operation
At the heart of precision gearboxes lies their ability to facilitate smooth and accurate motion control, which is essential for the performance of advanced machinery. The primary function of a gearbox is to convert input speed and torque into a desired output, a task that requires impeccable synchronization of gears. This synchronization minimizes backlash—the slight movement between gear teeth—resulting in enhanced positional accuracy and repeatability. Such precision is crucial in applications like CNC machines, where even minute deviations can lead to significant errors in the production process.
Precision gearboxes also play a vital role in reducing noise and vibration, contributing to the overall stability and reliability of machinery. By ensuring that gears mesh seamlessly, these gearboxes mitigate the wear and tear that typically occurs in less refined systems. The reduction of friction and heat generation further enhances the longevity of both the gearbox and the machinery it powers. Additionally, many precision gearboxes are equipped with integrated lubrication systems, which maintain optimal operating conditions and reduce maintenance requirements. This combination of high efficiency and low maintenance makes precision gearboxes indispensable in settings where continuous and reliable operation is non-negotiable.
Innovations and Future Directions in Industrial Gear Solutions
The ongoing advancements in industrial gear solutions are poised to further transform the manufacturing automation sector, promising even greater efficiency and precision. As industries continue to push the boundaries of technology, the demand for gearboxes that can accommodate higher loads, faster speeds, and more complex motions is growing. Innovations such as smart gearboxes, which incorporate sensors and real-time monitoring systems, are emerging as game-changers. These intelligent systems can predict maintenance needs, detect anomalies, and optimize performance dynamically, reducing downtime and extending the lifespan of machinery.
Additionally, the integration of advanced materials and lubrication technologies is enhancing the durability and performance of precision gearboxes. The development of new alloys and composites, along with innovative lubrication methods like self-lubricating coatings, ensures that gearboxes can operate under harsher conditions with minimal maintenance. The focus on sustainability is also driving the design of more energy-efficient gear systems, which not only reduce operational costs but also contribute to environmental conservation. Also, the customization of industrial gear solutions is becoming increasingly prevalent, allowing manufacturers to tailor gearboxes to their specific applications. This bespoke approach ensures that each gearbox meets the unique demands of its operating environment, whether it's in heavy machinery, precision tools, or automated production lines. As the fourth industrial revolution, or Industry 4.0, continues to unfold, the role of precision gearboxes will be integral in enabling smarter, more responsive, and more efficient manufacturing processes.
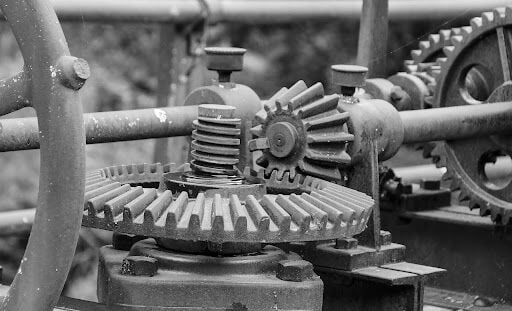
Transforming Efficiency and Performance
The integration of precision gearboxes into machinery has revolutionized various industries by significantly enhancing efficiency and performance. In the manufacturing sector, precision gearboxes enable automated systems to operate with exceptional speed and accuracy, reducing production times and increasing output quality. This has led to the development of more sophisticated manufacturing techniques, such as 3D printing and automated assembly lines, which rely heavily on the precision and reliability of these gear systems.
In the field of robotics, precision gearboxes are integral to the development of advanced robotic arms and autonomous vehicles. These applications demand precise control over movement and positioning, which would be unattainable without the high accuracy provided by precision gearboxes. In aerospace, the ability of these gear systems to withstand extreme conditions while maintaining performance ensures the safety and efficiency of aircraft and spacecraft. Furthermore, the renewable energy sector benefits from precision gearboxes in wind turbines, where they help maximize energy conversion efficiency and ensure the reliable operation of turbine blades under varying wind conditions.
The Role of Digitalization in Gearbox Innovation
Digitalization is playing a pivotal role in the evolution of industrial gear solutions, driving significant advancements in design, monitoring, and maintenance. The integration of digital technologies, such as the Internet of Things (IoT), artificial intelligence (AI), and digital twins, is enabling the development of smart gearboxes that offer real-time performance monitoring and predictive maintenance capabilities. These smart systems can collect and analyze data on gear performance, wear, and environmental conditions, providing valuable insights that help prevent failures and optimize maintenance schedules.
Moreover, digital tools are enhancing the design and testing phases of gearbox development. Advanced simulation software allows engineers to model and test gear systems under various conditions, identifying potential issues before physical prototypes are built. This not only speeds up the development process but also ensures that the final product meets the highest standards of precision and reliability. The adoption of digitalization in gearbox innovation is transforming how manufacturers approach design and maintenance, leading to more efficient, resilient, and intelligent industrial gear solutions.
Precision gearboxes are a fundamental element in the advancement of manufacturing automation, providing unparalleled accuracy, efficiency, and reliability. From sophisticated design processes to innovative functionalities and profound impacts on various industries, these gear systems are essential for modern machinery. The continuous evolution of industrial gear solutions, driven by customization and digitalization, promises to further enhance the capabilities of manufacturing processes, paving the way for more advanced and efficient industrial operations. As technology progresses, the significance of precision gearboxes will only grow, cementing their role as a cornerstone of industrial innovation and efficiency.
Here are some other articles reated to your search:
(0) comments
We welcome your comments
Log In
Post a comment as Guest
Keep it Clean. Please avoid obscene, vulgar, lewd, racist or sexually-oriented language.
PLEASE TURN OFF YOUR CAPS LOCK.
Don't Threaten. Threats of harming another person will not be tolerated.
Be Truthful. Don't knowingly lie about anyone or anything.
Be Nice. No racism, sexism or any sort of -ism that is degrading to another person.
Be Proactive. Use the 'Report' link on each comment to let us know of abusive posts.
Share with Us. We'd love to hear eyewitness accounts, the history behind an article.