The realm of medical devices is as diverse as the individuals it serves, encompassing everything from basic bandages to sophisticated imaging systems. Behind every medical device is a meticulous manufacturing process shaped by stringent quality controls, advanced technologies, and the relentless pursuit of perfection. Understanding this process is crucial for professionals in the field, investors, patients, and anyone with a vested interest in the future of healthcare technology. Join us as we explore the multifaceted process of manufacturing medical devices.
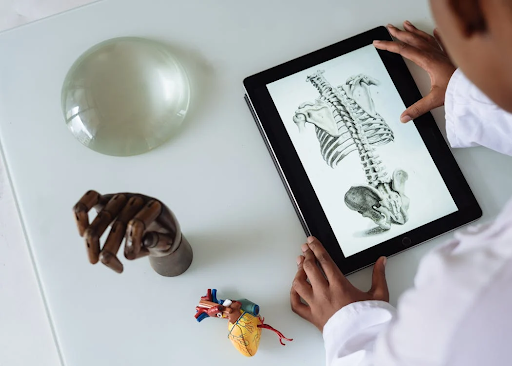
Conceptualization and Design
The genesis of a medical device starts with a groundbreaking idea. This conceptual phase is dominated by research and development teams who brainstorm, analyze needs and set forth design parameters. It involves creating a plethora of prototypes and engaging in extensive testing, ensuring that the nascent device can meet the medical needs it seeks to address. Computer-aided design (CAD) plays an invaluable role here, allowing designers to visualize and manipulate their creations in a virtual space.
Material Selection
Selecting the appropriate materials is pivotal to the success of a medical device. Materials must not only be durable but also biocompatible, ensuring they can safely interact with the human body. Metals, plastics, ceramics, and advanced composites enter into a careful selection process where factors such as strength, flexibility, and reaction to exposure to bodily fluids are considered. The chosen materials form the bedrock upon which the device's reliability and longevity are built.
3D Printing in Medical Device Manufacturing
Once the purview of prototyping alone, 3D printing, also known as additive manufacturing, has now taken a frontline position in the production of medical devices. This technology allows for the layer-by-layer construction of components, offering unparalleled precision and customization. From patient-specific implants to complex device components, 3D printing for medical devices boasts a reduced time-to-market for innovative medical solutions. The benefits of 3D printing, like minimal waste and the capability to create intricate designs unachievable by traditional methods, make it a staple in modern medical device manufacturing.
Molding and Shaping
Molding and shaping processes are critical steps where the selected materials take form. For plastics, processes such as injection molding and blow molding are common, while metals might be subjected to machining or forging. These techniques must be flawlessly executed to ensure the integrity of the device and its components. Advanced robotics and computerized systems are often deployed to achieve the high precision required by medical standards.
Assembly and Automation
With individual components ready, the assembly process begins--often the result of precise planning and support from engineering services. This stage is crucial for ensuring that each product meets the required standards of quality and performance Here, both manual dexterity and automation play a part, creating a symbiotic relationship between human skill and technological precision. For intricate devices, skilled technicians meticulously assemble delicate parts with care and expertise, often requiring specialized tools and a steady hand. This level of craftsmanship ensures that each component fits perfectly and functions as intended.
Meanwhile, automated systems are employed for repetitive or less delicate tasks, enhancing the speed and consistency of the assembly line. These systems use advanced robotics and precise programming to handle tasks such as screwing, welding, or placing components in exact positions. The growing trend of automation in assembly lines helps in reducing human error and increasing efficiency, ultimately leading to higher productivity and lower costs. Additionally, the integration of smart technologies and real-time monitoring systems allows for continuous improvement and quick adjustments, ensuring that the assembly process remains optimal and reliable.
Testing and Quality Assurance
Testing is an uncompromising phase in medical device manufacturing, where devices are put through a rigorous battery of examinations to ensure they meet all necessary performance criteria. This phase is critical to ensuring that the final product is both effective and safe for use. Quality assurance teams work meticulously alongside regulatory guidelines to verify various aspects such as device efficacy, safety, and reliability. These teams often include engineers, scientists, and compliance experts who bring a wealth of knowledge and experience to the process. In some cases, simulated environments are created to assess how a device will perform under specific conditions, such as extreme temperatures or high-stress situations. These simulations help identify potential issues before the device reaches the market, thus safeguarding the health and well-being of future users.
Sterilization and Packaging
Before a medical device can be shipped to hospitals or clinics, it must undergo a thorough sterilization process to eliminate any potential microbial contamination that could pose a risk to patient health. This crucial step ensures that the device is safe for use in medical procedures. Various sterilization methods are employed based on the device's material tolerance and the nature of its usage. Common techniques include gamma irradiation, which uses high-energy photons to eradicate microorganisms; ethylene oxide gas, which permeates the device to destroy pathogens; and autoclaving, which utilizes high-pressure steam to achieve sterilization. Each method has its own advantages and suitability depending on the specific materials and design of the device. Following sterilization, the device is carefully sealed in specialized packaging to preserve its sterile state, ensuring it remains uncontaminated until it reaches its destination and is ready for use in a clinical setting.
Regulatory Compliance and Distribution
Regulatory compliance is a thread that weaves through every step of medical device manufacturing. Governments enforce stringent regulations and certifications, such as the FDA's approval in the United States, to protect patients. Once a device has cleared all regulatory hurdles, it is distributed through channels that depend upon the healthcare network's exigencies and the manufacturer's business model.
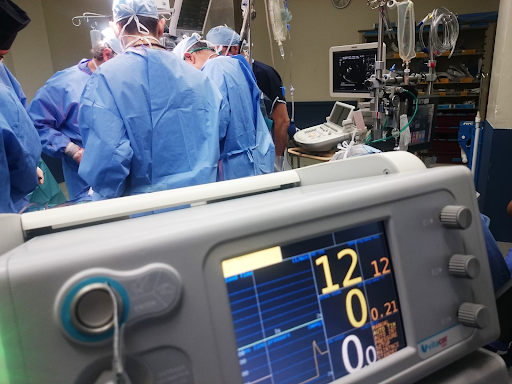
The manufacturing of medical devices is a testament to the harmonious confluence of technology, craftsmanship, and ethical standards. Every device that rolls out of the production line embodies a promise - a promise of quality, care, and the inexorable march towards better healthcare for all. For those intrigued by the confluence of innovation and well-being, the process outlined here provides a glimpse into the painstaking craftsmanship and technological prowess invested in moving medical devices from the drawing board to doctor's offices and operating rooms around the world.
In this landscape of life-affirming inventions, maintaining a heartbeat in sync with the deliberate and delicate processes of device manufacture not only saves lives but elevates the human experience. Through understanding and appreciation of the complexity involved, we can better appreciate the devices that support health and the pivotal roles they play in the modern medical ecosystem.
(0) comments
We welcome your comments
Log In
Post a comment as Guest
Keep it Clean. Please avoid obscene, vulgar, lewd, racist or sexually-oriented language.
PLEASE TURN OFF YOUR CAPS LOCK.
Don't Threaten. Threats of harming another person will not be tolerated.
Be Truthful. Don't knowingly lie about anyone or anything.
Be Nice. No racism, sexism or any sort of -ism that is degrading to another person.
Be Proactive. Use the 'Report' link on each comment to let us know of abusive posts.
Share with Us. We'd love to hear eyewitness accounts, the history behind an article.