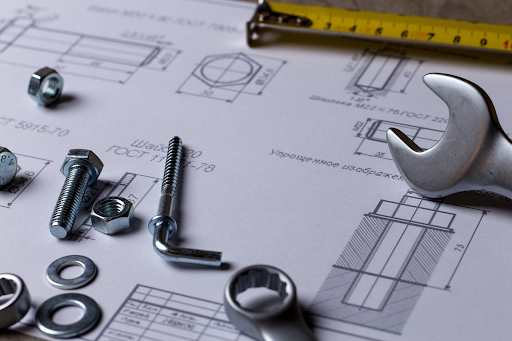
What Are Head Screws?
Head screws are a type of fastener with a head at one end and a threaded shaft at the other. The head can come in various shapes and sizes, designed for different tools and purposes. Common types include hex heads, slotted heads, and Phillips heads. For commercial use, M10 cap head screws can provide strong, reliable fastening solutions for various applications, including machinery assembly, structural support, and equipment manufacturing. They are primarily used to join two or more components together, providing strong and reliable connections in various industrial applications.
Types of Head Screws
Understanding the different types of head screws is essential for selecting the right one for your project. Some common types include:
Hex Head Screws: These screws have a hexagonal head, allowing for easy installation using a wrench. They're often used in heavy-duty applications due to their strength and resistance to stripping.
Flat Head Screws: Designed to sit flush with the surface, flat head screws are ideal for applications where a smooth finish is required. They can be driven into the material at an angle.
Pan Head Screws: With a rounded top and a flat bearing surface, pan head screws provide a larger area for distribution of load. They’re commonly used in electronics and appliances.
Socket Head Screws: These screws feature a cylindrical head with a hexagonal socket, making them suitable for high-strength applications. They allow for greater torque than traditional screws.
Choosing the right type of head screw can affect the performance and aesthetics of your final assembly.
Material Considerations
The material of head screws plays a critical role in their performance. Common materials include:
Steel: Steel screws are durable and cost-effective, making them a popular choice in various applications. They are often treated with coatings for corrosion resistance.
Stainless Steel: For environments prone to moisture or corrosive elements, stainless steel screws offer excellent resistance to rust and corrosion. They are ideal for outdoor and marine applications.
Aluminum: Lightweight and corrosion-resistant, aluminum screws are often used in industries where weight is a concern, such as aerospace and automotive.
Brass: Brass screws provide a unique aesthetic and are resistant to corrosion, making them suitable for decorative applications.
Choosing the right material based on environmental factors and the intended use of the screws is essential for ensuring longevity and performance.
Load Capacity and Strength
Load capacity is a crucial factor to consider when selecting head screws. The strength of a screw depends on its diameter, length, and material. For heavy-duty applications, ensure the screw can withstand the required load without failing. Always refer to the manufacturer's specifications and guidelines to determine the appropriate load capacity for your project.
Diameter and Thread Pitch: The diameter of a head screw significantly impacts its load capacity. A larger diameter allows for a greater surface area that can withstand tensile and shear forces. Additionally, the thread pitch plays a role in distributing the load along the screw's length, with finer threads offering more grip in softer materials and coarser threads providing better-holding power in harder materials.
Material Strength: Different materials exhibit varying strength characteristics, which directly affect load capacity. For example, stainless steel screws offer high tensile strength and corrosion resistance, making them ideal for applications in challenging environments. On the other hand, softer materials like aluminum may be more suitable for lightweight applications where load requirements are less demanding, but they may not hold up under excessive strain.
Length Considerations: The length of the screw is equally important when determining load capacity. Longer screws may provide better anchoring in thicker materials, but they can also increase the risk of bending or breaking under heavy loads. Conversely, shorter screws may be less prone to bending but could fail to provide adequate grip if not properly anchored, leading to potential structural issues.
Applications in Different Industries
Head screws are used in various industries, including:
Construction: In construction, head screws are often used to fasten structural elements, such as beams and trusses, ensuring stability and safety.
Automotive: In the automotive industry, head screws secure engine components, body panels, and various mechanical systems.
Electronics: Head screws are essential in electronics, holding together devices and ensuring they function correctly.
Manufacturing: In manufacturing, head screws are used in machinery and equipment assembly, playing a critical role in maintaining operational efficiency.
Understanding the applications of head screws in your specific industry will help you make informed decisions about which fasteners to use.
Installation Techniques
Proper installation of head screws is vital for ensuring a secure connection. Here are some key techniques:
Pre-drilling: For harder materials, pre-drilling holes can help prevent splitting and ensure proper alignment.
Using the Right Tools: Always use the appropriate tools for the type of screw you're working with. Using the wrong tool can strip the screw head or damage the material.
Torque Specifications: Adhere to the manufacturer's torque specifications to avoid over-tightening, which can lead to material failure.
Checking Alignment: Ensure that components are correctly aligned before fastening. Misalignment can lead to stress and potential failure over time.
By following these installation techniques, you can maximize the effectiveness of head screws in your projects.
Environmental Impact and Sustainability
In today's industrial landscape, the environmental impact of materials and fasteners is an increasingly important consideration. When selecting head screws, you should think about the sustainability of the materials used. Opting for screws made from recycled metals or sustainably sourced materials can significantly reduce your project's ecological footprint. Additionally, consider the end-of-life disposal of these fasteners - many manufacturers are now producing screws that can be easily recycled.
Maintenance and Inspection
Regular maintenance and inspection of head screws in industrial applications are essential for safety and performance. Look for signs of wear, corrosion, or loosening. Replace any damaged or compromised screws immediately to avoid potential failures. Consider implementing a routine inspection schedule, especially in critical applications where screw integrity is vital.
Understanding head screws is crucial for anyone involved in industrial applications. By familiarizing yourself with the different types, materials, load capacities, applications, and installation techniques, you can make informed decisions that enhance the efficiency and safety of your projects. Whether you're working in construction, automotive, electronics, or manufacturing, the right head screws can make all the difference in your assemblies.
(0) comments
We welcome your comments
Log In
Post a comment as Guest
Keep it Clean. Please avoid obscene, vulgar, lewd, racist or sexually-oriented language.
PLEASE TURN OFF YOUR CAPS LOCK.
Don't Threaten. Threats of harming another person will not be tolerated.
Be Truthful. Don't knowingly lie about anyone or anything.
Be Nice. No racism, sexism or any sort of -ism that is degrading to another person.
Be Proactive. Use the 'Report' link on each comment to let us know of abusive posts.
Share with Us. We'd love to hear eyewitness accounts, the history behind an article.